Toy Fulfillment: 3 Supply Chain Strategies to Consider
This year over 59% of holiday shoppers will be purchasing toys. With the average consumer expected to spend about $800, this is a substantial time of the year for toy manufacturers and retailers. The pressures of keeping costs low while responding to greater delivery demands and options are amplified during the holidays, but need to be addressed year round. Poor fulfillment can quickly ruin a birthday or special occasion. To prevent your toys and your brand from being synonymous with disappointment, optimizing your fulfillment operations and supply chain is imperative. Here are three strategic tips that can keep your supply chain lean, fulfillment accurate and inventory efficient.
- Upgraded technology: A lot of issues that toy manufacturers and retailers run into stem from heritage systems and legacy software. Tapping into the new technologies that address customer concerns and expectations can be difficult with these tools. Implementing technology and processes that enhance visibility can keep your supply chain lean and running smoothly.
- Leverage brick and mortar locations as fulfillment centers: A lot of big companies are utilizing their inventory and store locations to meet consumer demands. This strategy is creating the opportunity to keep pace with on-line only operations by cutting shipping costs, shipping longer into the holiday season, and even offering same-day delivery. Drop shipping directly from store locations can be an efficient use of inventory as well as a great option for consumers.
- Outsource when and where necessary: Recognizing your strengths and utilizing outside skills and resources to improve your operation, specifically your supply chain, can create a tremendous advantage. Even newer strategies, like drop shipping from store inventory, can benefit from fine tuning. Too much can disrupt customers visiting the store, too little can become an expensive undertaking. Understanding how fast inventory is moving from both the storefront and distribution center is key. Scaling human resources, space and technology for peak times can also be more effective from a third party.
As more purchases shift from the store to the web, effectively handling those orders and the increased demands that accompany them has never been more important. As your brand grows and peak seasons arrive, having the ability to scale, avoid errors and keep costs down can become difficult. Leveraging the expertise and experience of a third party logistics company can relieve these pain points. With a focus on technology and a customized process that fits your supply chain needs, Barrett Distribution Centers has been creating fulfillment solutions for over 73 years.
Recent Blog Posts
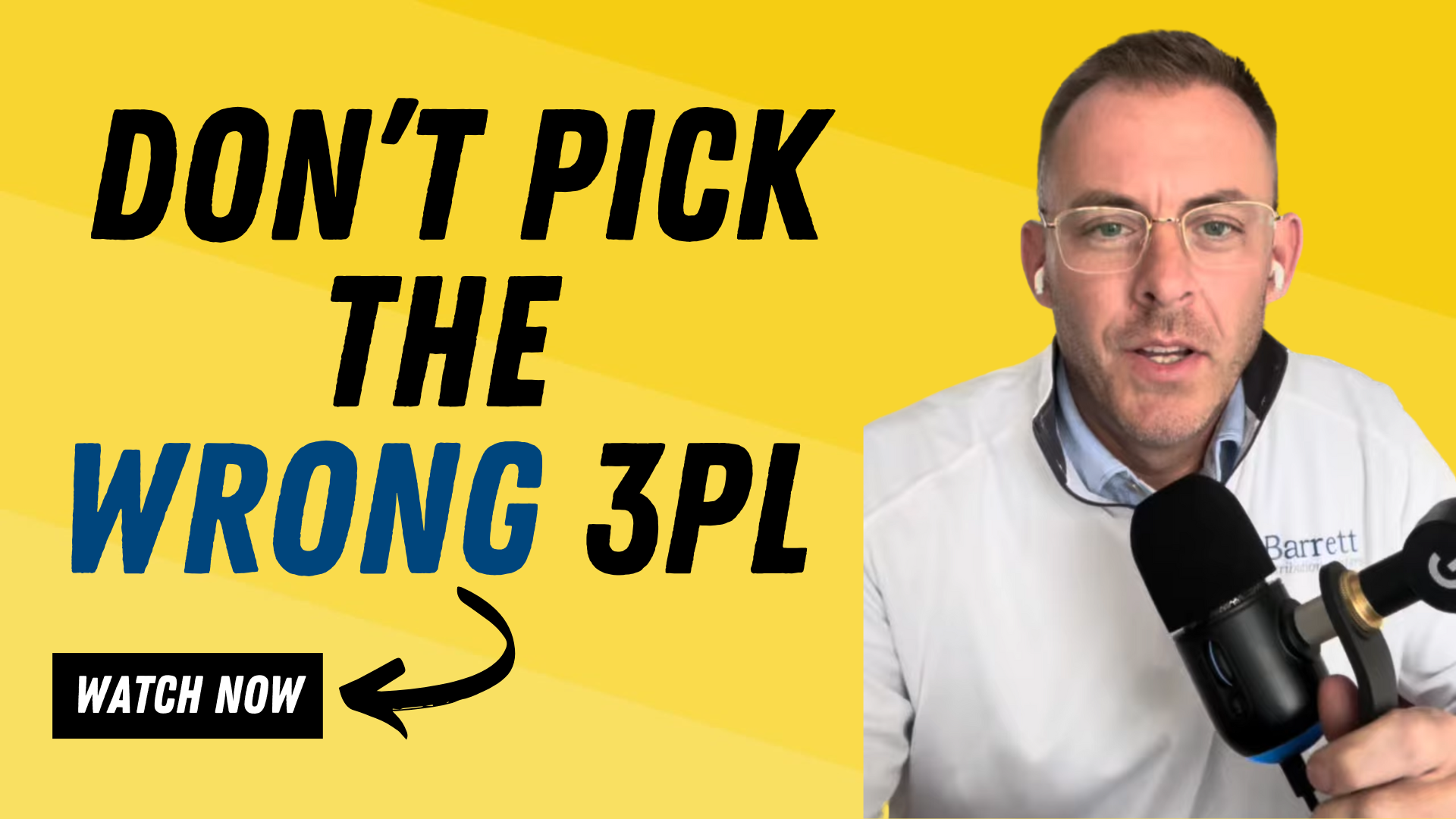
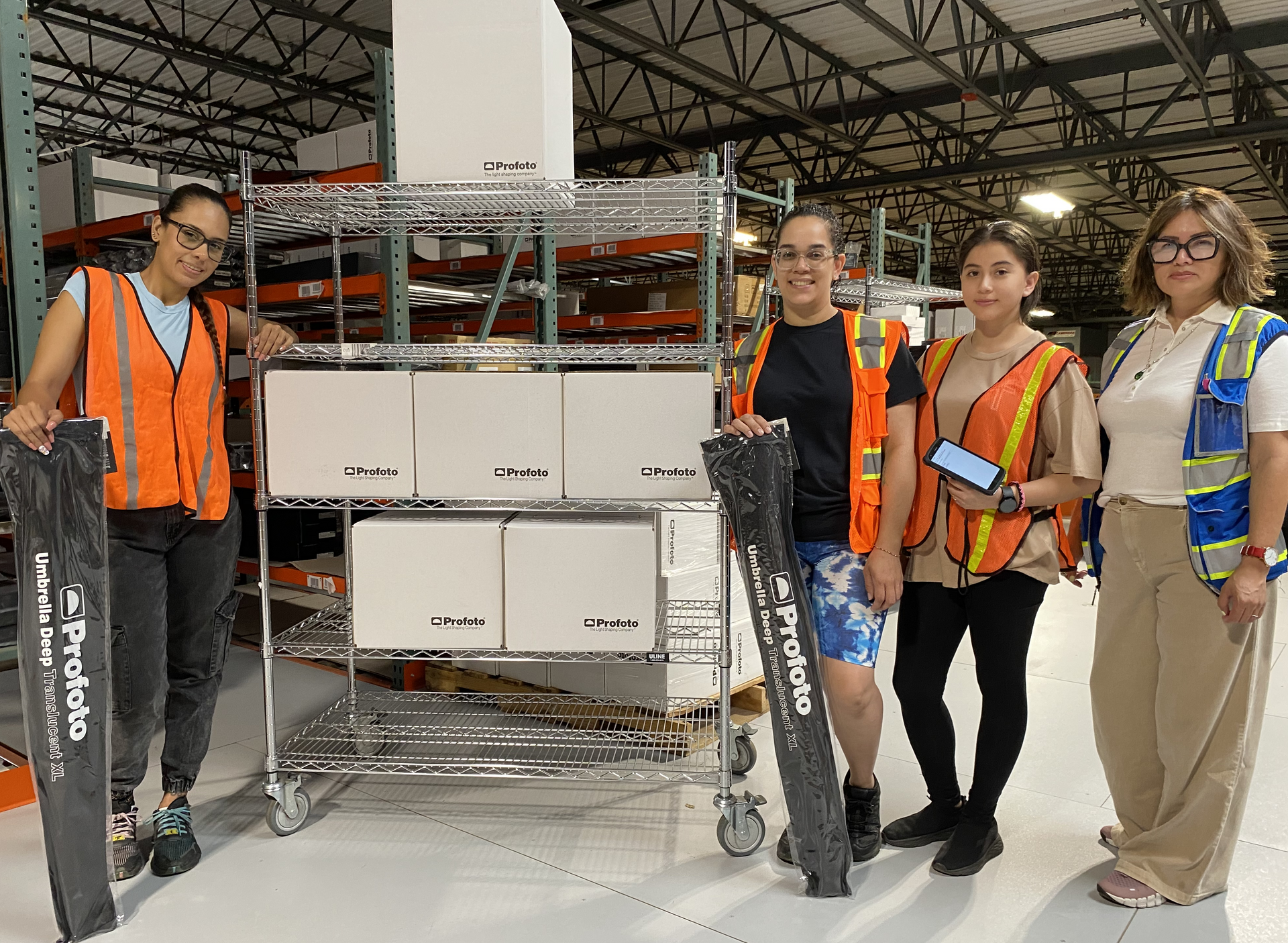
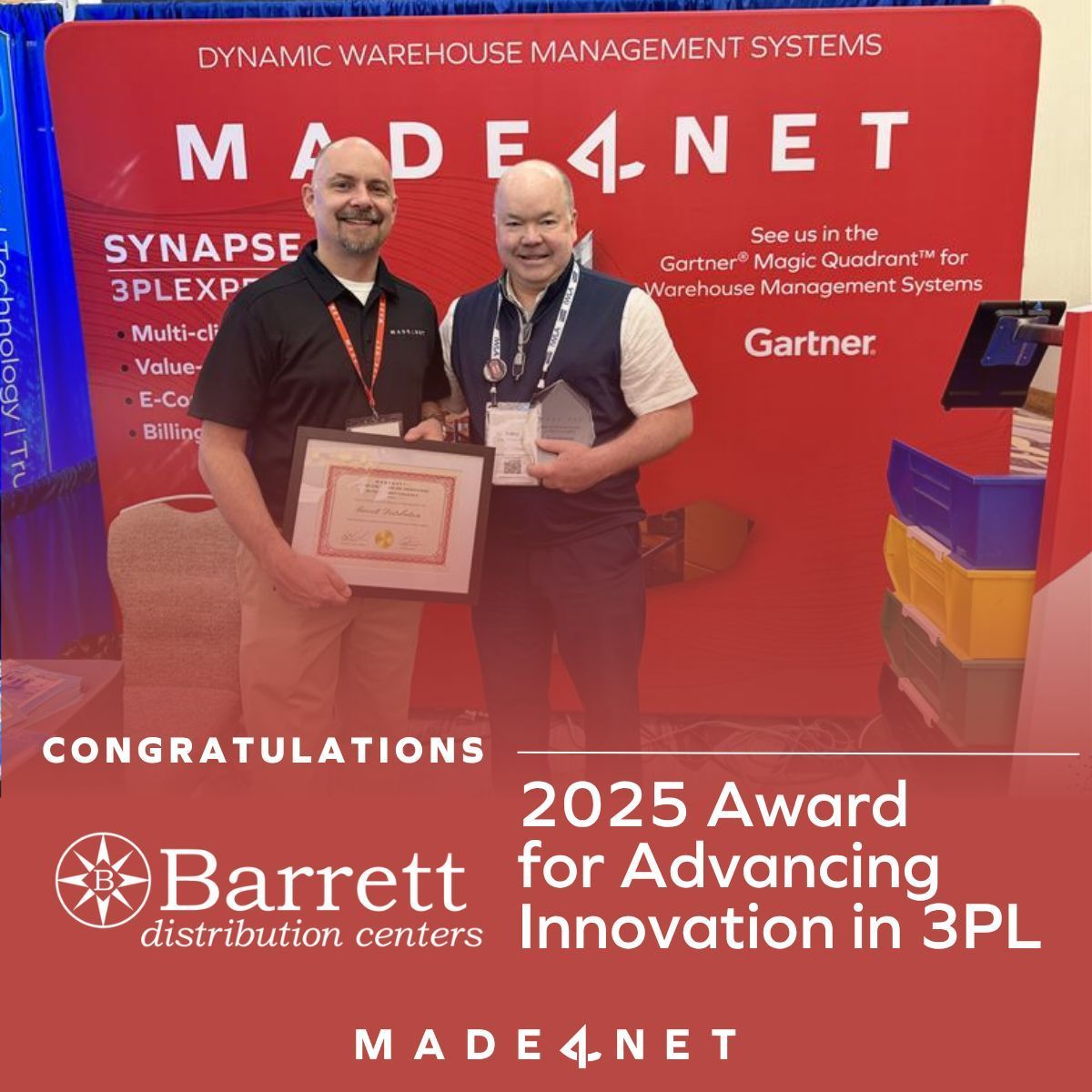