3 Supply Chain Contingency Planning Tips for Medical Device Companies
The recent months have brought some intense weather to all corners of our country. From the “Polar Vortex” last winter to violent tornadoes across the Midwest to Hurricane Arthur, each new day and week holds something new and potentially challenging. The only thing constant about weather is change. Theses volatile climate patterns unfortunately bring more than wind, snow, rain and lightning. Unfortunately these events cause a spike in emergency room and hospital visits. There have already been 41 tornado fatalities in 2014, according to NOAA. In fact during the Polar Vortex, Modernhealthcare.com reported that hospitals in Detroit brought in additional staff on multiple occasions to treat ER patients.
To make things more challenging, these additional visits and demands on hospital staffs and medical groups are often coupled with constraints on resources and accessibility. Over the 4th of July weekend, Hurricane Arthur left over 40,000 people with power and even caused a part of North Carolina Hwy. 12 to buckle on Hatteras Island. Last winter’s frigid temperatures and precipitation forced numerous surgeries and procedures to be rescheduled or cancelled. While organizations have contingency plans and redundancies in place to account for these scenarios, what back up strategy is there to account for supply chain complications?
The timely and precise demands that define medical device logistics needs to be maintained, especially in times of great need. Investing the time, energy and resources into contingency planning is like buying insurance. Hopefully you’ll never need it, but having the plans and process in place when these challenges arise can be the difference between life and death. These 3 elements can be implemented into your medical device supply chain, allowing your organization to persevere in the most difficult times.
- Be pre-emptive: While weather plays a major role in the disruption of services and the addition of constraints on resources, there are many other factors that could disrupt your supply chain. Manmade disasters, business decisions and governmental factors, just to name a few. However by having a finger on the pulse of what is happening around your organization can allow you to forecast possible problems. Notifying the key logistical partners that make up your supply chain is key. Ensure everyone is on the same page and ready to find answer to potential questions.
- Increase your essential supplies: To combat any lags or disruptions to your supply chain, having an abundance of the most necessary and important supplies stocked and accessible is crucial. Any device that you’ve been without in a similar situation should be maintained at a higher level to prevent a recurrence. While your bottom line is still a major consideration, you don’t have to throw your inventory management plan out of whack, but you do need to account for any delays.
- Supplier audits: This is a key element in maintaining visibility. Understanding and seeing the process your logistic partners leverage, and more importantly the results, can show the imperative steps to protect it in an emergency, as well as where other resources can be pulled to create a lean, agile fulfillment plan when necessary.
Supply chain contingency is a key element within your overall strategy. Identifying and responding to potential risks can mitigate a substantial threat to not only your operations, but your community. In an Inbound Logistics survey, 73% of participating companies claimed to have experienced a supply chain disruption. 32% of those said it took over 1 month to recover. Working closely with your supply chain personnel and partners is a critical step in preparing for the worst. With a focus on visibility and a track record of results, Barrett Distribution Centers has the technology, man-power and resources to play a key role in your contingency planning.
Recent Blog Posts
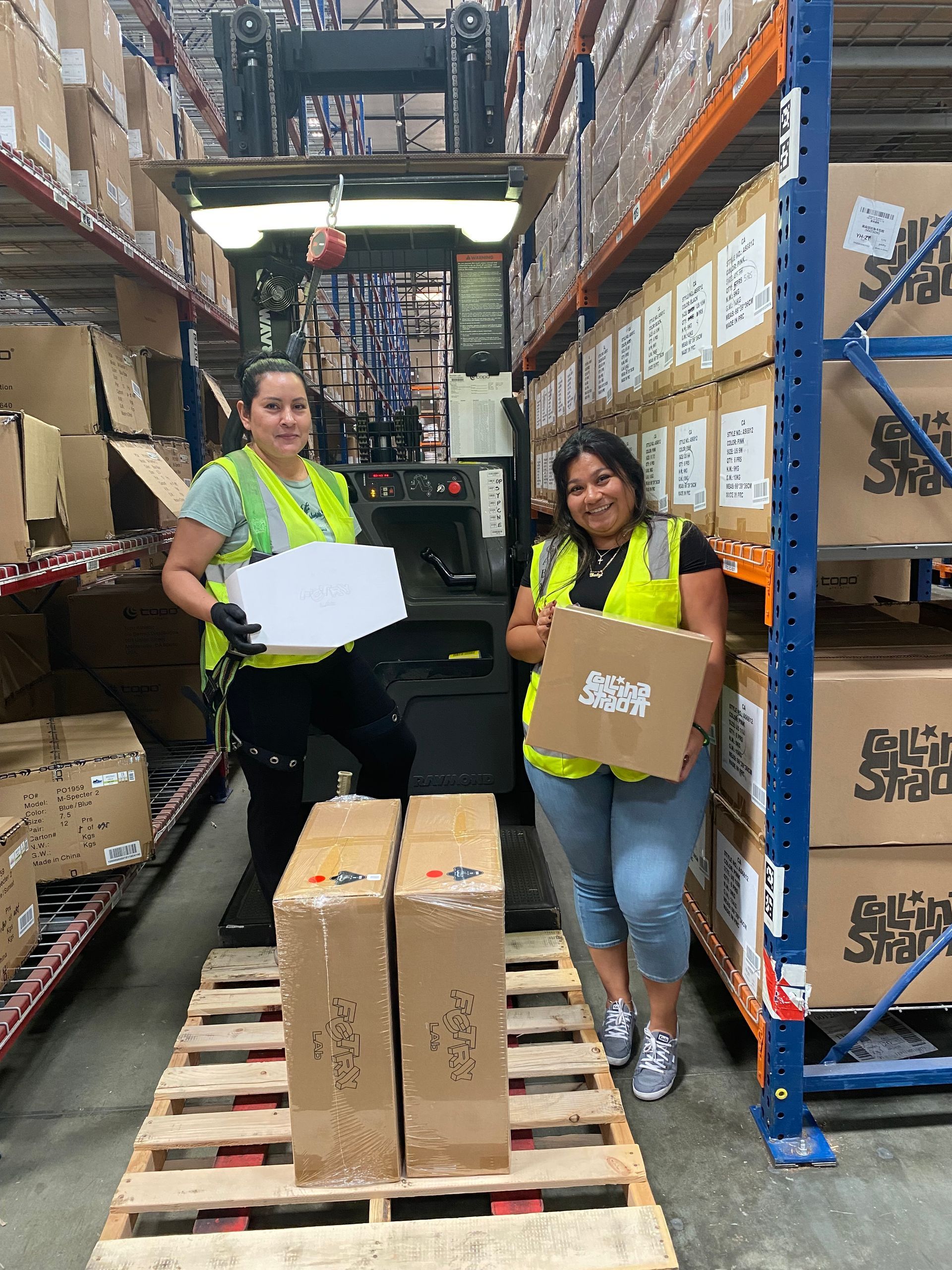
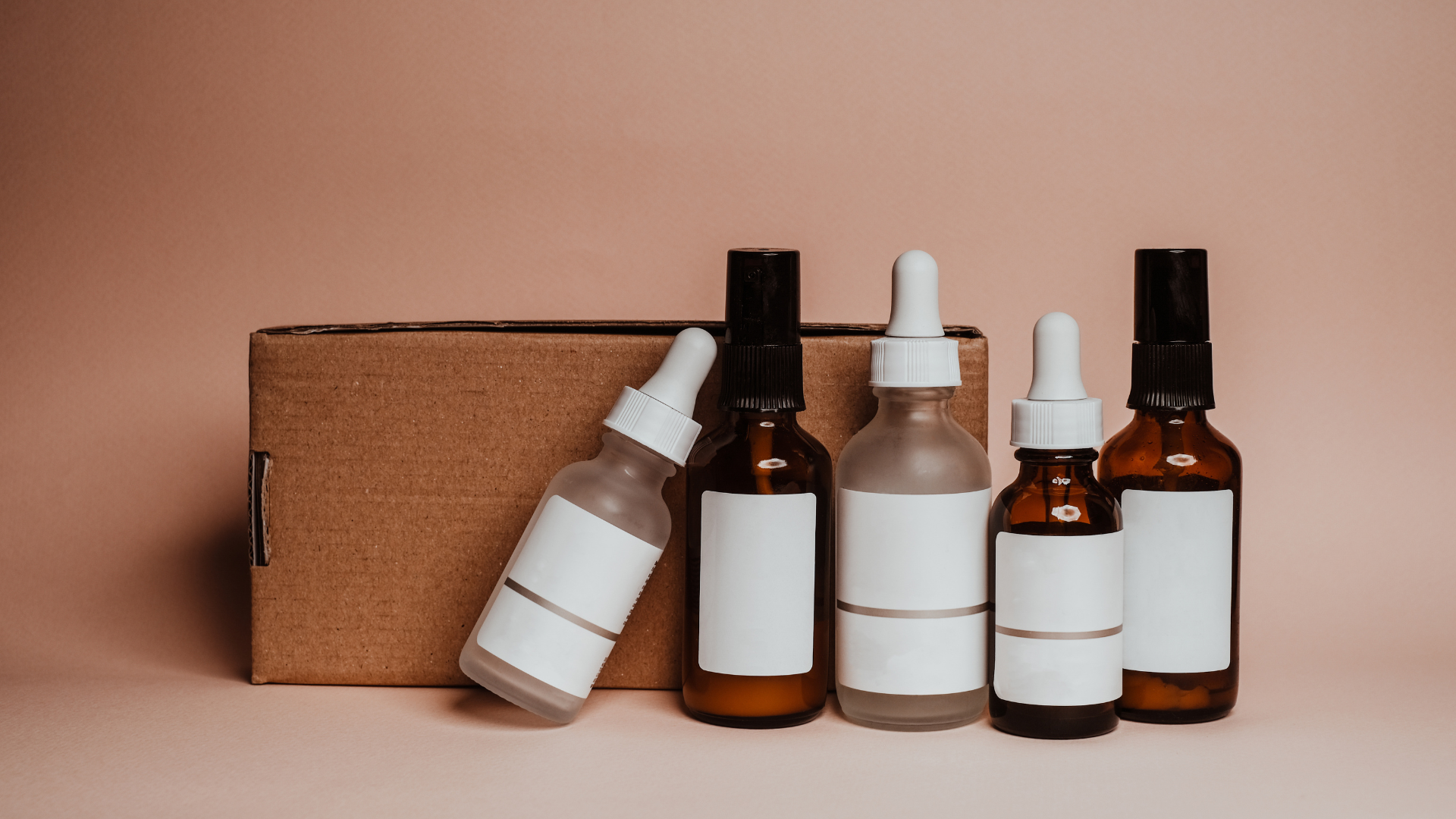